
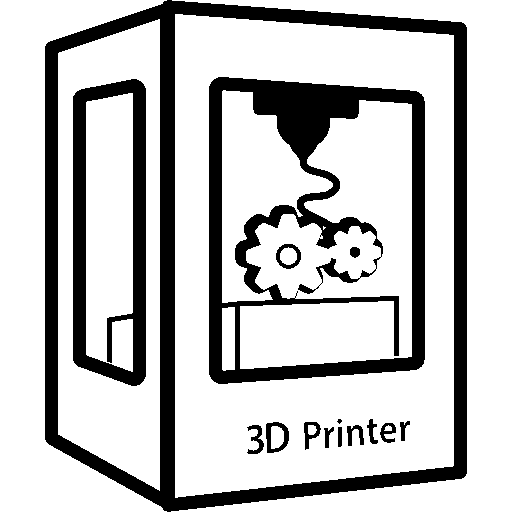
How about a 3D-printer that prints its own z-axis?
How about a 3D-printer that prints its own z-axis?
Plastic is the wrong material due to moisture building up inside and some other pitfalls.
First of all: Legal is the bare minimum.
If you run a contest or sweepstakes and set out rules you are bound to them. Ignoring them like Prusa did exposes you up to liability claims.
You’re mad that the contest was moderated?
More the opposite. The sloppy way they moderate it to the point where they don’t even bother to remove comment spam below the contest description page.
Voters voted on the submissions they liked the most. Get over it. Voters voted on the submissions they liked the most. Get over it.
That’s not how it works. There is no public vote.
Honestly I stopped reading. Something about a paid part integration that you got mad about because it’s heavily discounted and you can submit photos even if you don’t have one or something?
Just read the comments here: https://blog.prusa3d.com/contest-experiential-robotics-challenge_97306/
Dozens feel like this isn’t a good choice.
Btw. I don’t take part in them but it is still very ugly what they do. Similiar you don’t need to buy Nestle to understand that Nestle might be problematic in some aspect.
For Germean voters there is the WahloMat to help with the voting choice (a dozen of questions and in the end shows how much overlap there is with all the parties): https://www.wahl-o-mat.de/europawahl2024/app/main_app.html
The major issue is that if you care about CopyRight: Party A. Easier to comply with regulation: Party B. Migration: Party C. Environment: Party D.
And all of the choices (A-D) have some very removed, prominent positions that you strongly oppose and in the end, have no clue what to elect and choose the least worst option and hope for the best.
I don’t lube the rails, it attracts too much dust. I still oil them to prevent rust.
The 50km figure is out of the HiWin application note at 30% load capacity. Even with 0% load it won’t go above 150km.
Looking at the Thompson-Link: It is for the self-lubrication block (long-term lubrication unit) which indeed has a much higher endurance. Raising maintenance intervals to roughly once per year. As far as I know, they are only available for MGN15 and larger.
has a maximum flow rate of 22 mm^3/s which limits it to about 250mm/s for 0.2mm layer height.
Divide the number by 5 which would be roughly every 100 print hour or two weeks of printing.
Marlin has this feature (time based) but most manefacturer didn’t enabled it.
Duet doesn’t have it
Klipper doesn’t (has a time counter so you could implement it easily).
Printers are pushing significantly faster acceleration these days with upto 50k mm^2/s and 1m/s is already real.
Works for me.
It allows me to post a make.
Some aspects of Printables are “wrong”. Contests are a total mess at the moment. I might make a serape post about it.
This? Looks like a glitch/bug. As far as I can tell this is only active on paid items which makes sense.
If cold pulls won’t work get a new nozzle. Filament of choice for this procedure is Nylon.
One of the alternatives could be THF to dissolve the plastic and go from there. Don’t know what Prusa charges for nozzles but it can’t be that bad to make this procedure worth it. After all it is a Prusa and not some industrial machine.
Improved but still not a match to Ultimaker Cura.
Prusa is very slow compared to Cura as PrusaSlicer needs every option checked including Geometry handling accurate to sometimes get 7 pcs. matching Cura performance. If the result is 7 or 6 pcs. depends on where the part originally was placed on the print bed (or luck? run to run variance?). Not a reliable software for nesting.
With fast and balanced setting it only does 6 pcs.
fast:
balanced:
accurate:
Default settings. Where is the option to rotate it?
Providing it manually with 90° rotated and using the auto arrange instead of fill bed: 5 pcs. Still not a great result.
Cars are a very high-vibration environment with km of wiring and some carrying high currents, flammable liquids and hot parts. With e-autos there is even more including a 50’000 Wh energy storage waiting to catch fire.
While cars do catch fire it is unlikely to the point where they don’t need fire suppression systems.
Some cars have fire suppression systems but those are race cars. Built differently to maximize performance. (or military vehicles)
Similiar there are 3D-printer that might benefit from a fire suppression system but the run of the mil 3D-printer won’t need it.
Not convinced? Look at CNC-mills or swiss lathes. Those are designed to run nonstop for years in a production environment at the highest speeds to maximize production. Most of them don’t have a fire suppression system (they do have a mist extraction/collector to prevent them from exploding).
I like BambuLab. They handled the issue seriously. Resolved it and now it is fixed.
What I meant with low end China is like QIDI-tech having exposed 230V (not fixing it), Tronxy choosing high and low voltage wires with the same color and no PE connection to the chassis, Ankermake having issues with the heatbed insulation (not fixing that either) and crushed wires. That’s just three examples and don’t expect that other companies are better. BambuLab is a rare exception.
Once you teardown “industrial”/professional machines the point of view changes: PE connections, strain relief, drag chain rated cables with appropriate bend radius, crimped ferrules instead of solder on wire ends, … they are built to last and run 24/7 without catching fire…
The best protection is a machine that is well build:
We have ovens in our kitchens that are designed to reach upto 400°C (for cleaning) and nobody is afraid of them catching fire. Why? They are engineered to be safe.
Similiar a 3D printer that has good engineering is safe and doesn’t require an automatic fire extinguisher.
If we talk about low-end China printers then the answer is they might not be as safe but the solution is to fix them instead of adding the fire suppression system.
The teeth is indeed a critical aspect. It has to be symmetrical as this assembly is mirrored to block the rotation in the other direction.
An alternative to this would be printing the spring with the contact surface separately and inserting it into this print (pause at layer height, insert part, continue print) allowing other geometries (that would overlap with the teeth if printed in place) and pretension. The downside is it’s a manual task and one more separate part to keep track of.
This is small and the tolerances of the center hub cause the teeths/“gear” to move approx. 0.3-0.5mm of centre. This means what you see in the CAD/slicer isn’t how it will look once printed. I had to narrow the gap down as much as I could to get the largest contact area. If you make it a sled on one side there is less material/surface area.
A further consequence is that the tip of it doesn’t touch anything as such you could remove the very tip to adjust the sound signature. The feeling is slightly changed but primarily this replaced the high-pitched plastic sound with a deep tone.
The nice aspect is that in the blocking position, it is a solid connection meaning it can take as much load as the teeth (tip) can support (hence the trying to maximize the contact area there). The spring element is only there to return this blocking “bolt” into position after a teeth passes through.
The issue with Weller is their price in a competitive market.
Considering no alternative the entry level Weller is fine. Ersa has their awesome itool with this really short distance between soldering iron tipp and finger grip: https://ts.kurtzersa.com/electronics-production-equipment/soldering-tools-accessories/soldering-desoldering-stations/produkt-details/i-con-pico-1.html
Performance: Weller and Ersa are more or less equal. For generic solder joints both are great. If there are high thermal mass and it isn’t possible to use a large tipp than the Hakko T12 is the superior technology. Changing tips on the Ersa (while not recommended by the manufacturer) can be done with the iron heated up and tool free within 5 seconds.
Ergonomics: 100% Ersa. The only reason it has been my daily driver for half a decade and is here to stay. Before this station I actually had a Weller.
JBC has a similar tool handle to the Ersa but those are very expensive with little benefit.
The price to performance king are genuine Hakko T12 tipps with a China station.